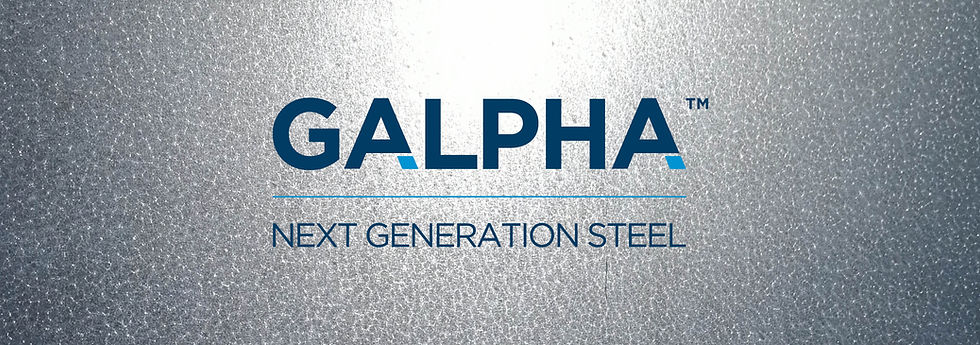
ABOUT GALPHA
HOT-DIP ALLOY COATED STEEL IN COILS & SHEETS
(95% Zinc, 5% Aluminium/Mischmetal - LA & CE Rare Earth Elements/Magnesium)
​
GALPHA is 3 to 7 times more corrosion resistant than zinc coatings of the same thickness, making the service life of a steel part significantly longer. You can also replace a zinc-coated part with a thinner GALPHA coating, thereby simultaneously offering improved welding and forming properties when compared to galvanised steel. Also when thinner GALPHA coatings are used, the amount of metres/sheets produced per MT is more than a thicker coated galvanised product, therefore improving cost-effectiveness.
The other benefit of using thinner coatings is a lower environmental impact when compared to thicker zinc coatings.
Corrosion resistance is excellent for GALPHA as it has very high sacrificial corrosion protection of the zinc and passivation of Aluminium, in addition, the added Magnesium has been found to have a beneficial effect on corrosion resistance, by stabilizing the low electric conductivity corrosion products of Zinc. There is also improved corrosion resistance for exposed steel surfaces including cut edge or damaged areas such as scratches or impacts. Full corrosion protection is also achieved in areas that have been heavily formed because the peeling tendency of low-friction and tightly bonded GALPHA is low.
COMPARISON OF COATING THICKNESS LOSS FOR REGULAR GALVANISED AND GALPHA

GALPHA is the first hot-dipped coating that is more formable than the steel it protects, as the Michmetal within the coating improves processing and as a result, formability is excellent.
GALPHA is very well suited to roll-forming, deep drawing, profiling and bending as the thin intermetallic layer at the interface of the steel and coating has a high crack resistance
The brittle intermetallic layer between the steel substrate and the regular hot-dip galvanised coating is virtually eliminated with GALPHA.



The formulation of 95% Zn/5% Al/Mischmetal/Mg alloy coating was first developed in 1970 in USA and further developed in Europe in the 1980s and it was found to have the best properties of both zinc, aluminium and magnesium coatings.
​
With the addition of Michmetals such as LA & CE Rare Earth Elements as well as Magnesium in low amounts, it was found through lab testing to have better forming and corrosion performance than similar formulations using higher amounts of Magnesium.
CHARACTERISTICS COMPARE GALPHA TO OTHER COATINGS

1=Lowest, 5=Highest
The standard coating for GALPHA is GALPHA275 in New Zealand, as it matches the coating thickness of the standard galvanised products it has replaced such as Z275, however, has a corrosion resistance which is 3-7 times higher.
When replacing galvanised with GALPHA we recommend using the following:
Galvanised Z275 = GALPHA135
Galvanised Z450 = GALPHA185
Galvanised Z600 = GALPHA275
YEARS OF USEFUL LIFE

YEARS TO RED RUST APPEARANCE
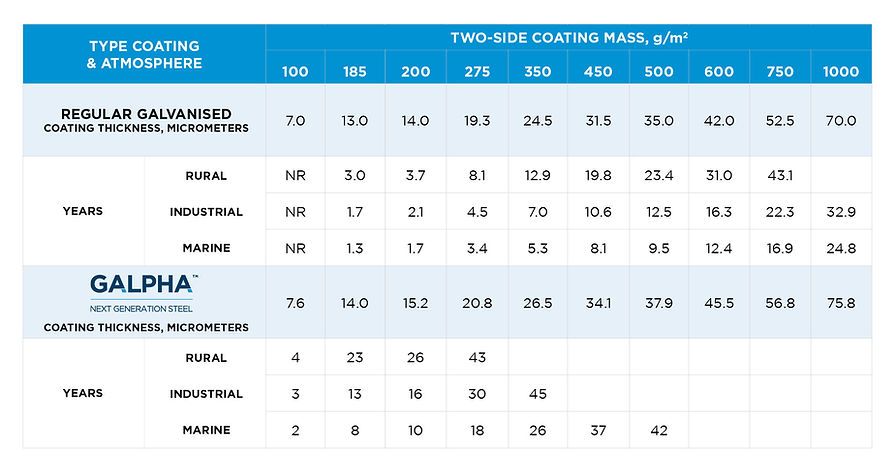
AVAILABILITY
​
​
​
​
​
​
​
​
​
​
​
​
Outdoor Exposure Testing within aggressive environments in New Zealand for 2 years - Coastal Marine & Geothermal in Rotorua
Results conclude that GALPHA outperformed galvanised with a rate of coating loss 3 times slower than galvanised in marine environments, and 2 times slower in geothermal.
​
After 2 years, the galvanised samples had severe white rust and after 3 years had significant red rust, whereas the GALPHA had none.
On profile bends where cracking had occurred down to the base material, GALPHA blocked the fissure with no undercutting, whereas galvanised steel corrosion undercutting had occurred to a distance several times the width of the original fissure.
Outdoor Exposure Testing within aggressive environments in New Zealand for 4 years - Coastal Marine & Geothermal in Rotorua
After four years at New Zealand test sites, both Severe Marine and Geothermal, results found that GALPHA was corroding at half the rate of galvanised steel.


LABORATORY SALT SEA SPRAY TESTS
The purpose is to predict the corrosion resistance (plane & formed). The test standard used was as per ASTM B 117 with a salt solution concentration of 5 +/-1% at a temperature between 33.3-36.1 degrees celsius. Sample condition was for plane: 75mm x 150mm and for 0T bending: 75mm.
Comparison of Salt Spray Test - Plane with GI (Z275, Z350) & GALPHA (GALPHA180, GALPHA275)


Comparison of Salt Spray Test - 0T Bending (up to red rust occurred)

Comparison of Salt Spray Test - Plane with GI Z275 & GALPHA180 (up to red rust occurred)

Comparison of Salt Spray Test - 0T Bending

APPLICATION PHOTOS

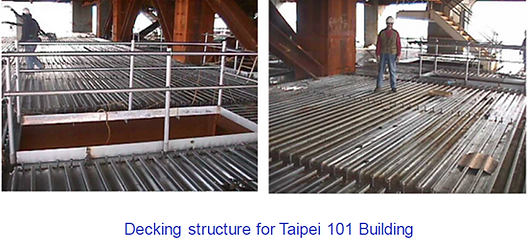

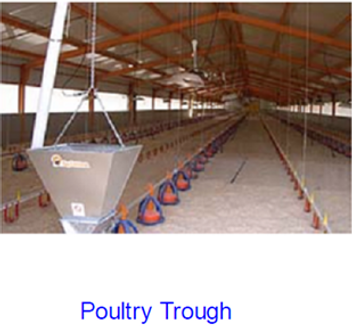
